Carbon Steel
I. Blast Furnace
![]() Blast Furnace |
![]() Discharge of molten Iron |
|
1. Blast Furnace
In the blast furnace, iron ore is reduced to pig iron through heating. The heating source is provided by burning coking coal. The whole procedure is computer controlled to maintain process stability.
II. Steel making
![]() De-Phosphorization |
![]() De-Carburization |
![]() RH Degasser |
2. Steel making
Pig iron retains some amount of undesirable elements such as Sulphur, Phosphorus and others. These elements are removed through multi stage specific reaction processes. Wakayama New Steel Making plant started operation in July 1999 as a state of the art facility respectful of the environment and can produce ultra clean steel with high productivity.
III. Billet & Pipe making
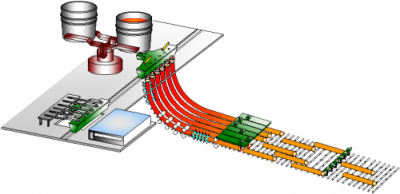
3. Casting
In continuous casting, Hot liquid metal is cast into solid semi-finished products in a variety of shapes. Among these, round bar "Billet" is used for seamless pipe making. Rectangular "Bloom" can also be used by applying a prior billet rolling process. Nippon Steel fully computerized continuous casting achieves improved yield, quality, productivity and cost efficiency. Billet Traceability to ladle is applied to maintain the best throughout quality control.